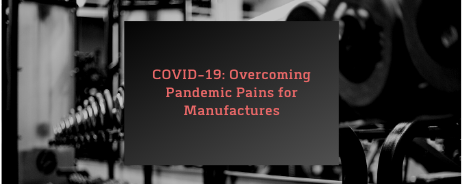
To Overcome Pandemic Pains, Manufacturers Are Changing The Way They Collect Data
While some businesses have fared surprisingly well during the pandemic, no company can claim that its productivity was entirely unaffected. Most manufacturers have faced especially significant challenges.
Per a recent survey from the National Association of Manufacturers (NAM), 78.3 percent of manufacturers expect that the pandemic will have a financial impact on their business. 53.1 percent of those surveyed anticipated a change in operations, while an astounding 35.5 percent faced supply chain disruptions.
For the industry’s decision makers, adapting to the “new normal” is easier said than done. That’s partly due to the way that manufacturers have collected and analyzed data to this point. By embracing new data collection technologies, some companies have found novel ways to weather the storm — and some have gained serious competitive advantages in a time of unprecedented uncertainty.
Reactive Data Tools Can’t Provide Insights During Major Disruptions
Social distancing measures and stay-at-home orders have exposed a significant issue for manufacturers: Data collection needs to be flexible to be useful. Many companies have relied on reactive analytics, which analyze the way production and supply chains have operated.
Note the past tense “have operated.” When components of a manufacturing process are suddenly disrupted, reactive analytics aren’t especially useful. Businesses need to stay nimble and make decisions to correct supply issues, optimize throughput, and address the changing needs of customers.
When you’re working with past-tense data, making these necessary changes can be difficult or impossible. Knowing how many units were shipped last quarter is, of course, essential — but when your client base shifts rapidly, it’s far more important to understand day-to-day trends.
Predictive Data Tools Can Fill In The Gaps (And Improve Throughput)
Some manufacturers have already implemented proactive analytic tools, which can generate reports that show the company’s performance in real time. These tools allow managers to make accurate predictions that shape the workflow and keep supply flowing.
For years, we’ve emphasized the value of these types of data tools. When everything is going smoothly, proactive tools improve coordination and communication, allowing productivity issues to be pinpointed and addressed. During a major disruption — for instance, a worldwide pandemic — predictive data collection tools are invaluable resources that allow managers to monitor their operations, implement new processes, and find the insights they need to make important decisions quickly.
Of course, there’s one significant hurdle to address: No two manufacturers are the same, and data collection tools need to be optimized for the company using them. There’s no one-size-fits-all approach to data collection, and when working with out-of-the-box software, minor inefficiencies can quickly become major hurdles.
When choosing predictive data collection tools, manufacturers should consider these factors:
- Remote Access – As many businesses learned during the first few months of the pandemic, when access is restricted to a single computer — or even a single group of computers — realtime monitoring becomes practically impossible. Predictive data tools should be accessible via any internet-connected device, and reports should be able to be generated remotely at a moment’s notice. With that said, data tools need appropriate security considerations. ERP platforms like Odoo allow flexible access for administrators, with numerous controls to prevent unauthorized access to certain features.
- Workflow Integration – Data analytics tools should be scalable to a company’s needs. When a software tool is customized for a particular workflow, scalability becomes much more achievable; users don’t need to sift through unnecessary metrics or unused features to get things done. Well-designed predictive data tools will actually simplify workflow, eliminating time-consuming tasks and giving managers more flexibility when dramatic changes need to occur.
- IIoT Features – The Industrial Internet of Things (IIoT) is more than a buzzword. When manufacturing equipment is able to convey crucial information — for instance, the amount of a certain material used at a given phase of the manufacturing process — those metrics can revolutionize the way that a manufacturer operates. However, in order to take advantage of IIoT equipment, data collection tools have to be able to collect and process that information efficiently. If a tool can’t provide realtime updates on key metrics, the value of IIoT equipment is severely restricted.
- Cost of Implementation – There’s a reason that many manufacturers haven’t switched to proactive data collection tools: It’s often a huge undertaking. Personnel need to re-learn key processes and change the way that they work — when the alternative is “continuing business as normal,” many companies opt for the simpler route.Ideally, the new tools can be implemented fairly quickly (and without significant growing pains). Customized data collection tools are suited to the users’ workflow, so they don’t carry enormous implementation costs. As soon as they’re put in place, they begin improving the business’s day-to-day.
Of course, there are dozens of other factors to consider, but as many manufacturers are learning, flexibility is critical. Proactive data tools give manufacturers the ability to shift suddenly in a downturn, and they’re just as valuable (if not more valuable) during periods of growth.
For years, we’ve helped businesses find the data collection tools that work for them. No two manufacturers work the same way, but customized solutions offer a quick return on investment by helping people work more efficiently. Data collection is performed in realtime, and key improvements can be made almost instantly. By building fully customized solutions (and helping our clients implement them painlessly), we’ve seen the results firsthand: Businesses improve their workflow, manage supply chains more effectively, and run leaner, more nimble operations.
Those operations are more capable of handling enormous disruptions — even when those disruptions are as unprecedented as what we’ve seen over the past few months. To learn how customized solutions can change your business and improve data collection, contact us today.